The energy storage pneumatic torque wrench is one of the mechanized hand tools powered by compressed air, while the hydraulic torque wrench uses hydraulic oil as the power source. It can be equipped with a manual pump or an electric oil pump, and a pneumatic torque wrench. It only works normally with a compressor. The hydraulic wrench can be pressed by a manual oil pump to work when there is no electricity. Because of the pressure factor, the torque of a pneumatic torque wrench is normally smaller than that of a hydraulic wrench. But Air Impact Wrenches are much faster
The pneumatic torque wrench is a major improvement on the original pneumatic torque wrench structure. Its characteristics are: large torque, light weight, and small air consumption. It is also one of the high-efficiency tools for disassembly and assembly of bolts and nuts. It is widely used in various industries such as petroleum, chemical industry, railway, bridge, metallurgy, electric power, mining, aircraft, ship, automobile and other public transportation.
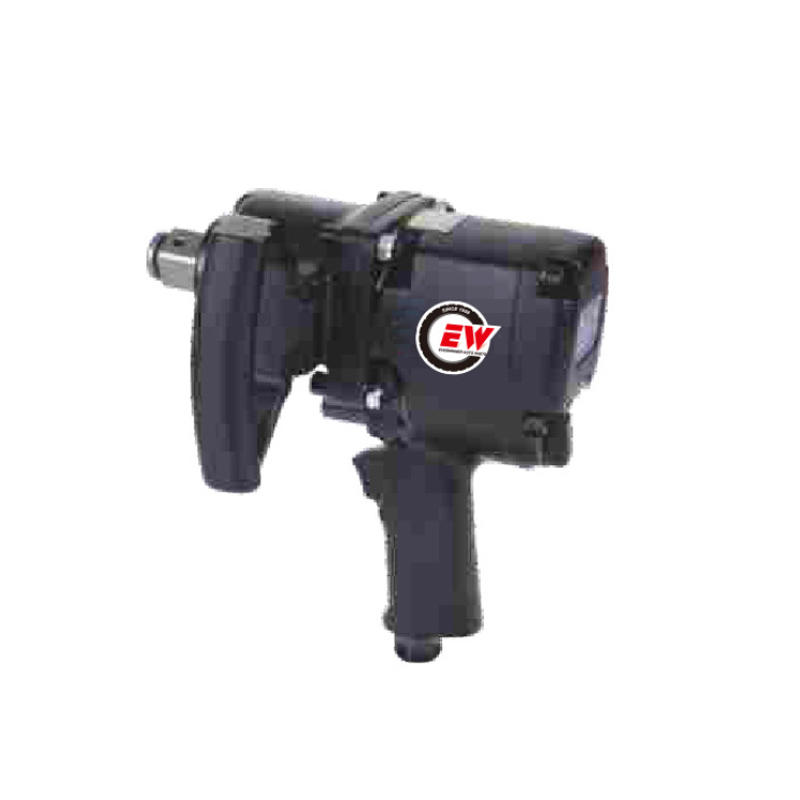
Precautions for use
In order to ensure the normal use of pneumatic torque wrenches, maximize their performance and extend their service life, attention must be paid to the use and maintenance of the pneumatic torque wrench.
1. The trachea should be intact. Before connecting the energy-storage pneumatic torque wrench, ventilate and blow out the internal organs of the trachea. The connection with the machine should be firm and sealed.
2. The pipeline air pressure should be maintained at 0.63 MPa and purified. Too high air pressure will increase the wear and tear and affect the life of the machine. The air pressure is too low and the performance is reduced.
3. There should be no air-water filter, pressure regulating valve and oil mister in the pipeline. When there is no lubricator in the pipeline, lubricating oil must be injected from the inner hole of the pipe 3-4 times per shift. No. 20 oil can be used in summer and No. 10 oil in winter.
4. Do not idling at high speed during use to avoid premature mechanical wear.
5. If a secondary impact is found during use, the machine should be shut down for inspection immediately, and it is forbidden to disassemble it on site (referring to unclean places), and should be sent to the repair department for inspection and repair in time.
6. The machine should be maintained once after a period of use (50-80 hours of cumulative use). The machine should be disassembled each time, and the parts should be washed with clean kerosene, blown dry, and coated with lubricating oil. The worn or damaged impact parts should be replaced in time. After assembly, inject a proper amount of lubricating oil for work test, and then it can be delivered to use after normal.
7. When you stop using it for a long period of time, use a wooden plug or a plastic plug to block the air inlet to prevent dirt from entering the machine.